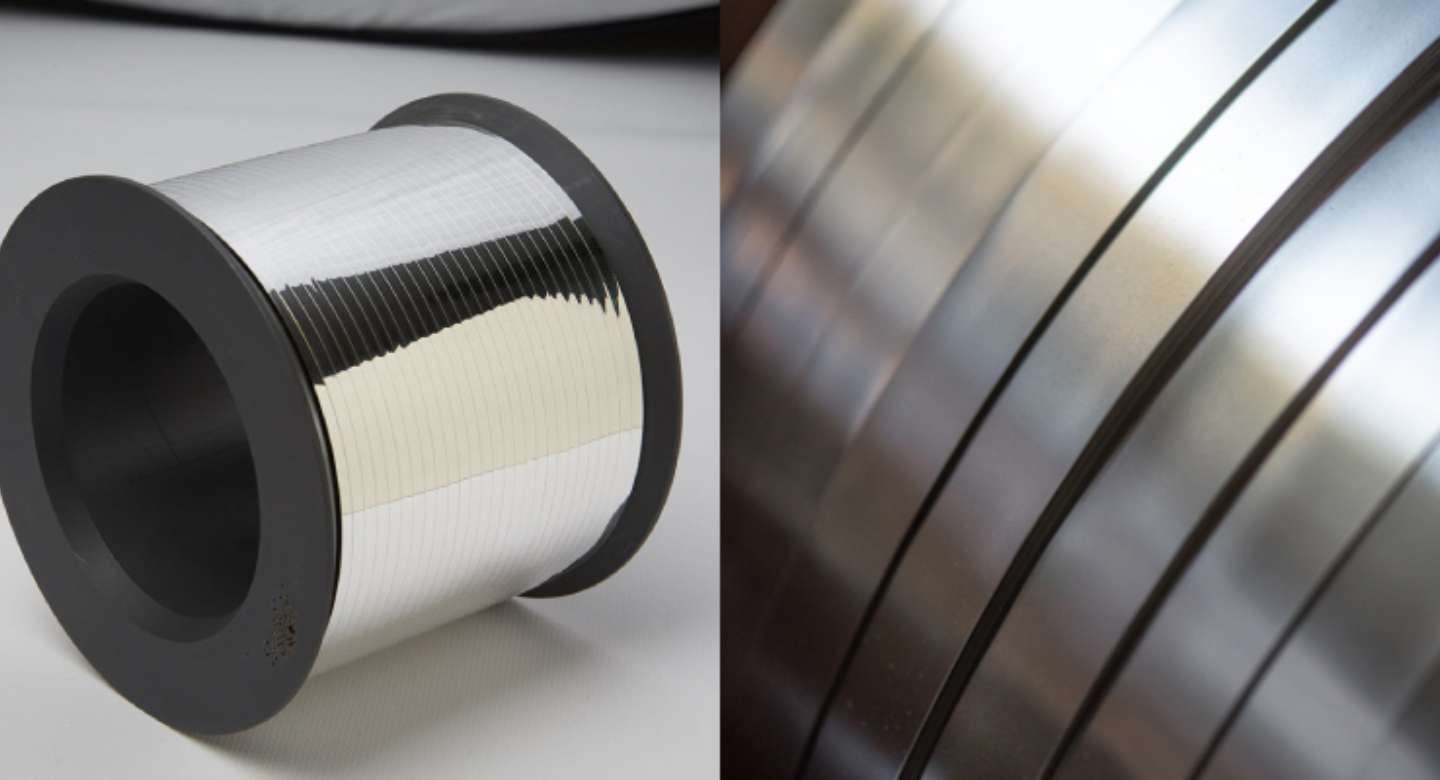
Considering Flat Wire as an Alternative to Strip
Modern precision slitters have the capability to generate narrow strip widths, reaching approximately .035" within specific thickness parameters. Nevertheless, it often makes sense to contemplate using flat wire as a viable substitute for strip material.
Today’s precision slitters are able to produce strip in very narrow widths, for example around .035” in a certain thickness range. In many cases, however, it is also often wise to consider flat wire as an alternative to strip.
Strip is often the most economical choice, particularly for wider sizes. As the width becomes narrower, the cost gap between Flat Wire and strip also narrows. At some point, it becomes less costly to choose a Flat Wire over a Strip or coil product. The cross-over width is dependent upon a few factors, including the material type, its mechanical properties, and the thickness. Width to thickness Ratio (Aspect Ratio) is also an important factor, both from a capability and cost standpoint for strip and flat wire processes.
The Basics of Flat Wire
While strip is produced by flat rolling very wide sections and then slitting to the desired width, flat wire is made by flat rolling round wire.
The rolling mill utilized to manufacture flat wire products is much smaller than a strip mill. Often multiple mill stands are linked together in series to achieve multiple reductions in a single processing step. Four-high mills, which have a “backup roll” to minimize roll deflection, are used in certain cases where separating forces are high, and flatness is important. Alternatively, two-high mills utilize two rolls contacting the metal to continue to work it flat.