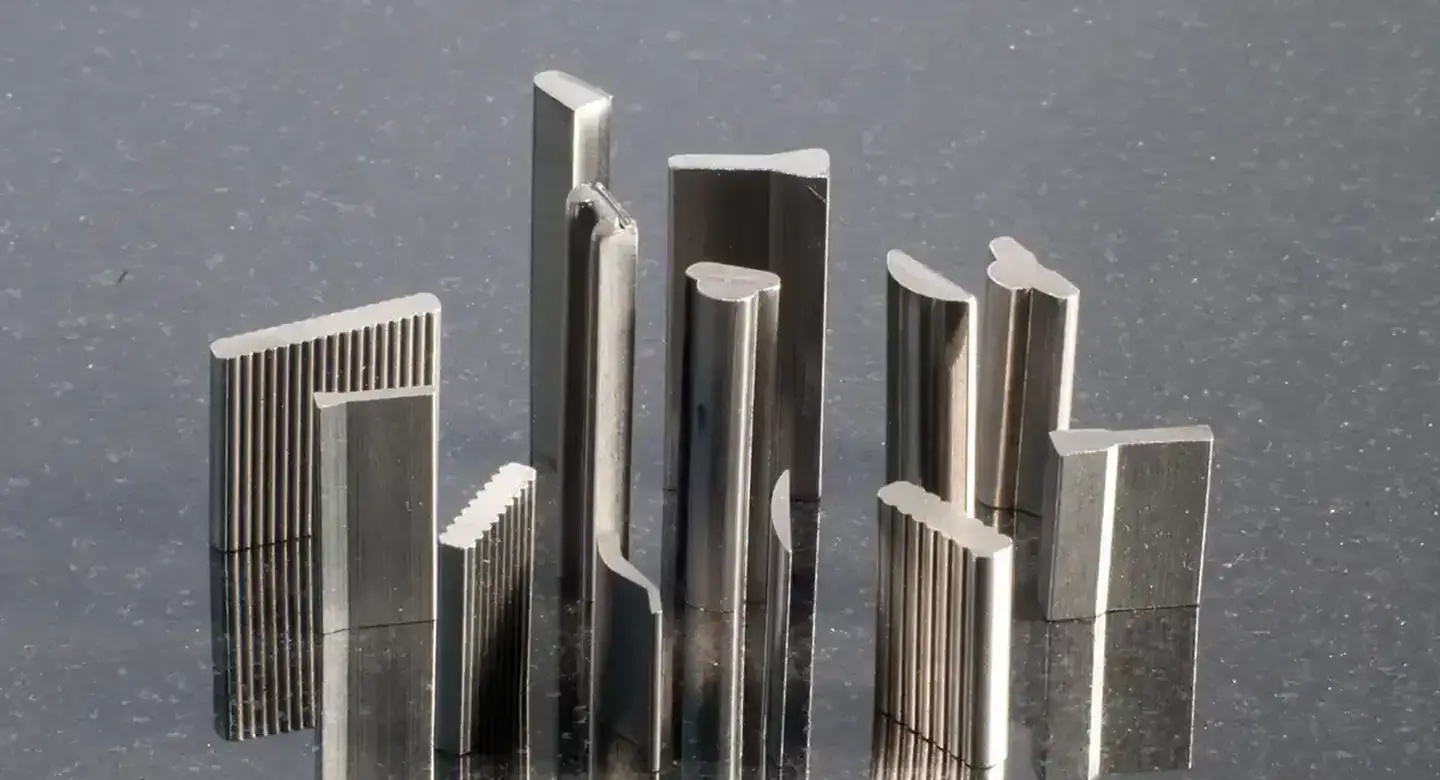
Machined vs. Shaped Wire Profiles for Optimal Manufacturing
Among the specialized manufacturing processes at Ulbrich Shaped Wire, net shapes distinguish themselves through their efficiency and minimal material waste, contrasting sharply with more traditional machining practices.
This guide will primarily explore Ulbrich's advanced net shape capabilities, showcasing how they optimize production and enhance performance. We'll also touch on the role of machined shapes to provide a comprehensive understanding of Ulbrich's innovative shaping techniques.
Join us to uncover how Ulbrich leads the shaped wire industry by focusing on precision profiled wire technologies.
What Are Machined Shapes and How Are They Produced?
Machined shapes refer to raw materials, typically bar products, precisely machined to their final shape. This process removes excess material through cutting, grinding, drilling, or other machining techniques. The raw material is initially manufactured with some allowance for machining to achieve the desired shape.
Machining raw materials allows for extremely accurate dimensions and are suitable for low-volume production. With machining, complex dimensions can be achieved. However, significant material is removed during machining, leading to higher costs, and additional machining steps mean a longer production time.
What Are Shaped Wire Profiles and How Are They Produced?
Shaped wire refers to wire that has been engineered into specific cross-sectional profiles, such as round, flat, square, or more complex shapes, to meet precise dimensional requirements.
At Ulbrich Shaped Wire, round wire is drawn, flattened and then shaped through a series of rolling operations. This process can include intermediate annealing to achieve the desired properties and dimensions. The result is a high-precision product that minimizes or eliminates the need for additional machining, making it suitable for various applications, from aerospace components to medical devices
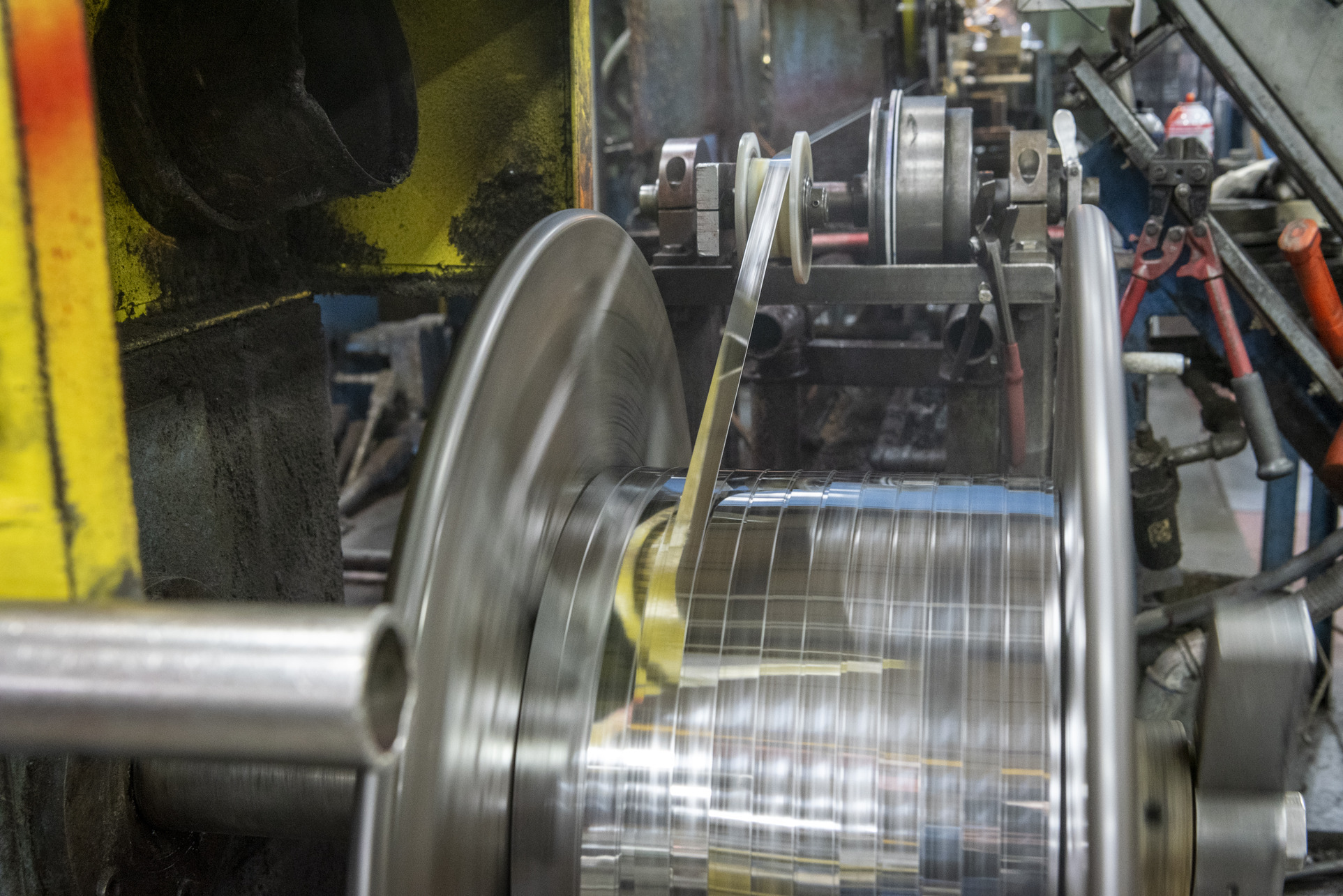
What Are the Advantages of Shaped Wire Profiles Compared to Machined Shapes?
Shaped wire profiles offer many advantages over machined shapes, including:
- Reduced Waste: Minimizing scrap material leads to cost savings in raw material procurement, recycling, and disposal.
- Faster Production: Fewer finishing steps mean shorter production times.
- Lean Manufacturing Benefits: Shape wire profiles help reduce the 8 Wastes (transportation, inventory, motion, waiting, overproduction, over-processing, defects, and skills), leading to more efficient operations.
What Advanced Manufacturing Capabilities Does Ulbrich Offer for Shaped Wire Profiles?
Ulbrich leverages state-of-the-art manufacturing techniques to meet the stringent demands of various industries. Our processes are specifically designed to favor the production of shaped wire profiles, reducing costs and minimizing waste while maintaining the highest quality standards.
Key Manufacturing Processes:
- Coil to Coil Processing: This method allows continuous production, enhancing efficiency and reducing material handling costs, making it ideal for larger production runs.
- Drawing: We use wire drawing to bring material down to size before shaping on Turks Heads mills.
- Cold Rolled Turks Head Processing: Shaping via Turks head processing allows for complex profile creation and efficient material usage.
- Precision In-Line Annealing: We use atmospheric-controlled precision in-line annealing to ensure consistent mechanical properties throughout the wire and provide a superior surface, enabling the production of complex shapes without compromising the metal’s integrity.
- In-House Tooling Capabilities: Our comprehensive in-house tooling center allows for rapid development and adaptation of tools to meet custom requirements, ensuring that each shape meets or exceeds all dimensional requirements.
- Precision Cut-to-Length: Whether you require precision tolerances or random lengths for easy handling, we'll cut it for you in-house.
Each step in our manufacturing process is closely monitored to maintain the highest level of quality, from the initial drawing of wire to the cold rolling process using Turks head mills to shape the wire into shapes. Our comprehensive in-house tooling center supports this detailed work, ensuring rapid responsiveness to market and client needs.
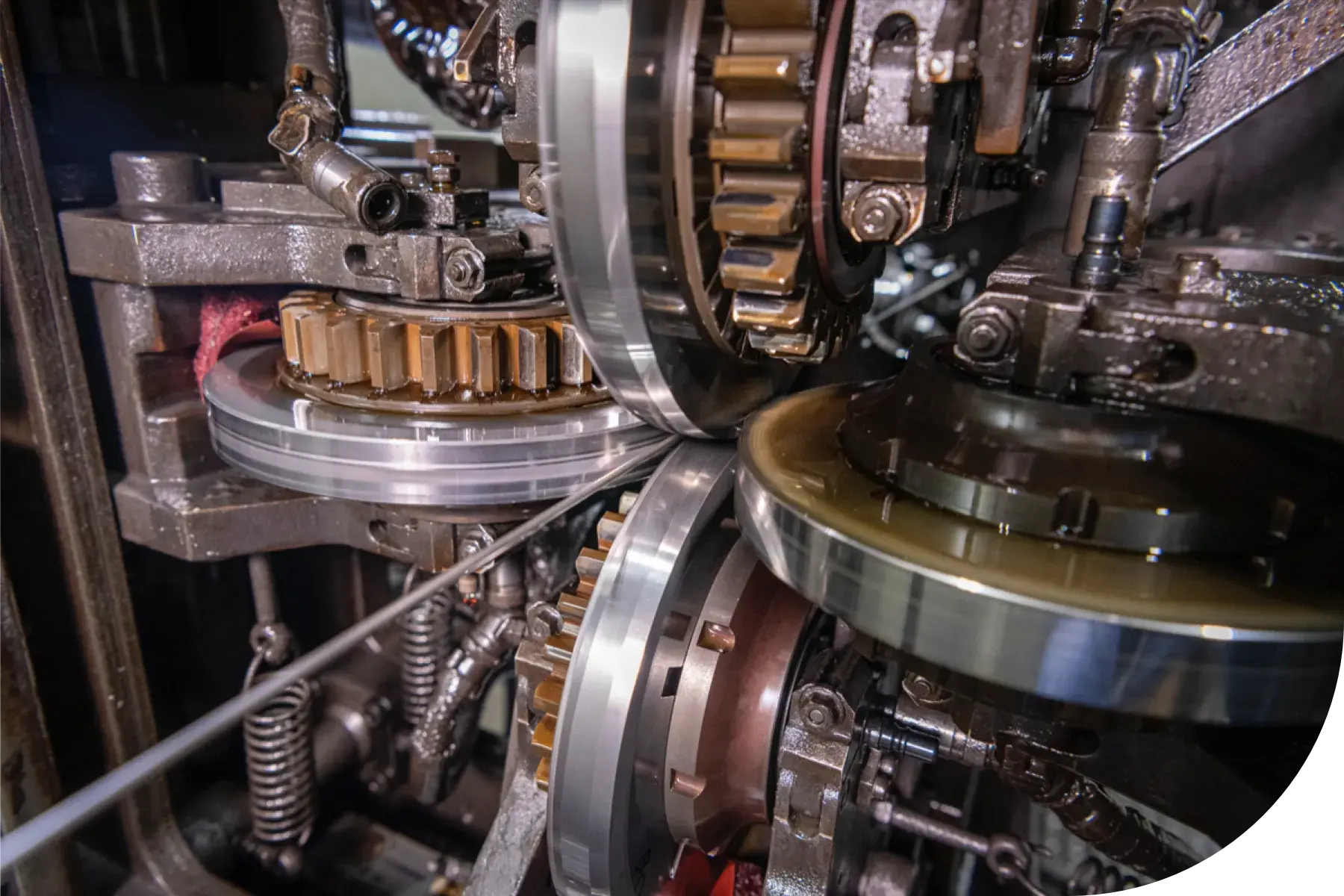
What Are the Benefits of Ulbrich’s Shaped Wire?
Ulbrich’s shaped wire production provides several benefits over traditional machining methods, particularly when it comes to manufacturing net shapes. Our advanced capabilities allow us to produce components that meet dimensional requirements, without additional machining.
Efficiency and Quality Benefits:
- Eliminate Secondary Operations: Our process designs significantly lower production time and costs.
- Precision Shaping: Turks head processing enables the formation of sharp edges and/or smooth transitions.
- Material Utilization: Net shape manufacturing at Ulbrich maximizes material use, with almost 100% of the material utilized in the final product, reducing waste and improving cost-efficiency.
- Operational Flexibility: The coil-to-coil process supports larger production volumes and frees up equipment for other manufacturing jobs, improving operational flexibility and capacity.
- Quality and Reliability: Quality is maintained through adherence to AS9100D, LCS, and ISO 9001 certifications, and state-of-the-art testing equipment ensures each shaped wire order meets industry standards.
When Should I Choose Shaped Wire?
Shaped wire manufacturing is preferable to traditional machined wire in several situations:
- Complex Geometries: When the wire shape is intricate or has complex curves, net shape processes can create these shapes more efficiently than machining. Example: Producing turbine blades with intricate airfoil designs.
- Material Conservation: Net shapes minimize material waste by closely approximating the final shape, reducing the need for excessive material removal. Example: High-cost materials like titanium or nickel alloys benefit from net shapes to conserve resources.
- Cost Efficiency: Net shapes reduce machining time, labor costs, and material expenses.
- Scalability: Net shape processes are scalable for large-scale production.
- Minimizing Post-Processing: Shaped wire creates forms to the final design, eliminating the need for subsequent machining.
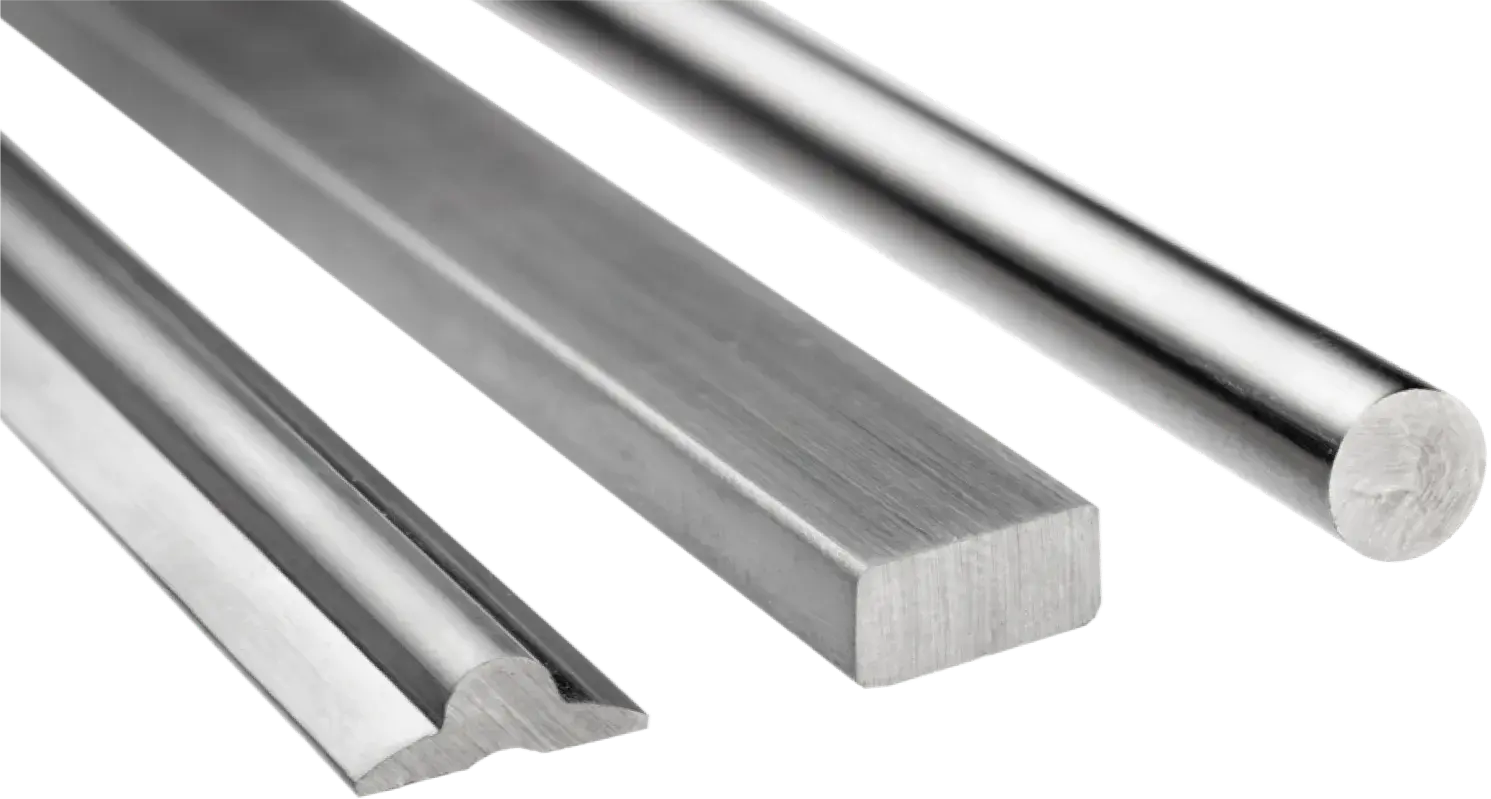
What Product Forms Does Ulbrich Offer?
Ulbrich provides a range of product forms tailored to meet the diverse needs of our clients, from oscillated spools and cut lengths to precision-cut lengths. Our expertise in shaping extends to both net and near-net shapes, ensuring that every product is perfectly suited to its application:
- Net Shape: Our net shape products are delivered in a completed form that meets all specified print requirements, ensuring they are ready to be used in your application without further processing. The vast majority of our products meet a net shape standard.
- Near-Net Shape: Our near-net shape products require only minimal additional machining to achieve details beyond our shaping capabilities. These forms can be provided either in near-net shape for further processing or potentially as finished parts through collaboration with an outside source.
We work with over 160 different alloys, offering a broad range of materials that meet precise industry standards and provide customized solutions for even the most challenging applications. This extensive range of materials, combined with our innovative forming techniques, allows for unmatched versatility and efficiency in seamlessly integrating our shaped wire into your manufacturing process.
What Are the Primary Industries and Applications for Ulbrich’s Shaped Wire?
Ulbrich’s shaped wire is engineered to meet the demanding requirements of various industries and applications. Whether it's aerospace, filtration, power generation, automotive, medical, marine, or defense, Ulbrich provides innovative wire solutions tailored to each sector's specific needs. With an unparalleled breadth of wire shapes and profiles, our products are designed for applications such as medical devices, oil and gas filtration screens, material for springs, and seal rings for various industries.
One of our key strengths is that we design and manufacture all our tools in-house, enabling us to accommodate an unlimited range of custom shapes. This adaptability ensures that Ulbrich’s shaped wire will be the right fit for your unique needs, no matter how specialized they may be.
Beyond Precision: The Ulbrich Advantage
Shaped wire manufacturing with Ulbrich offers benefits like minimal material wastage, reduced production costs, and high product quality. These processes enhance manufacturing efficiency, enabling the production of complex shapes with greater speed and less overhead.
We invite industry leaders and innovators to consult with our experts to explore how net shape capabilities can enhance your production processes. For further inquiries, request a quote or contact us today.