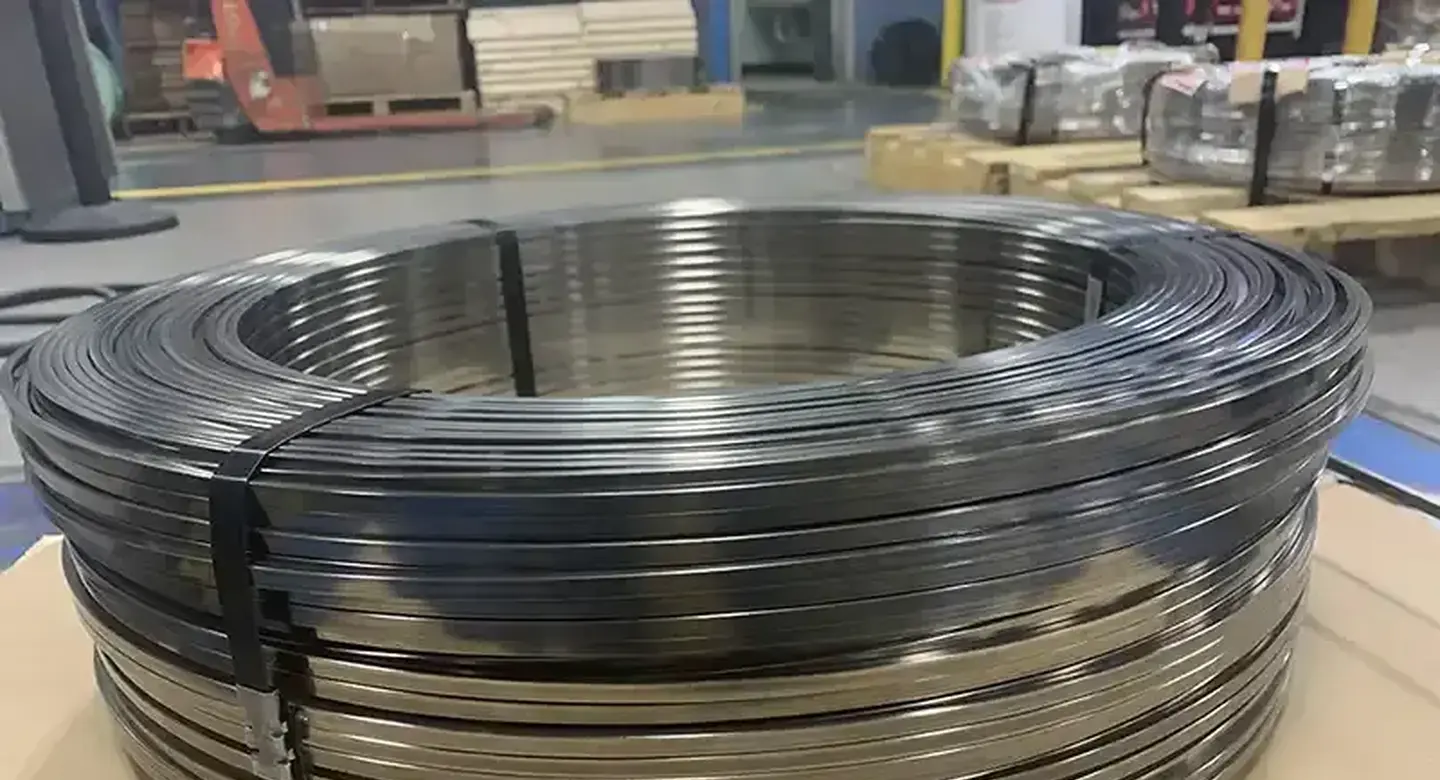
Metal Selection Guide: Strip Versus Flat Wire
With today’s precision slitters, it is possible to obtain strip products in widths as narrow as .035 inch, depending on thickness. However, when widths are this narrow, stampers are presented with another option – flattened wire.
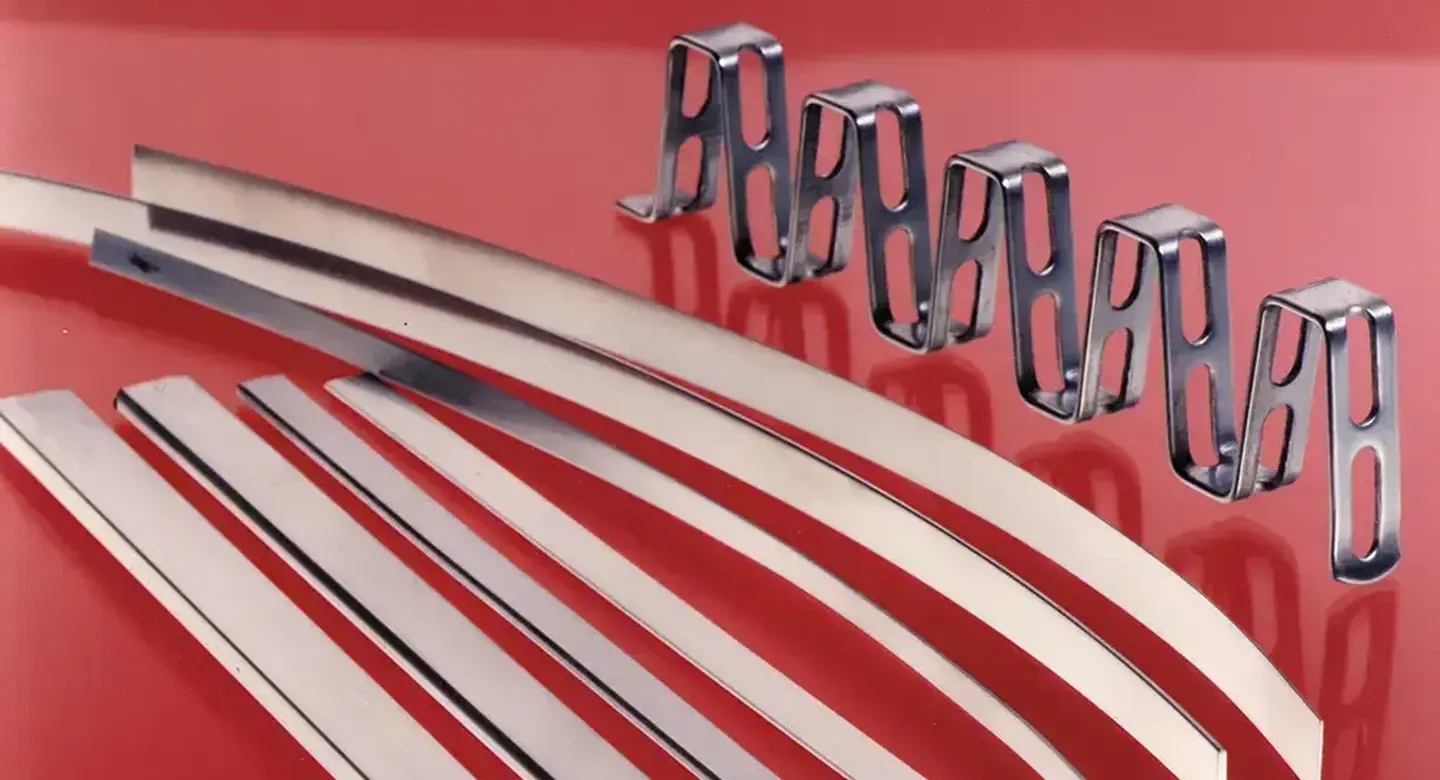
The similarities and differences in narrow width strip, one produced by slitting flat stock, the other by drawing wire through a mill, can be seen above. The four lengths on the left started as round wire; the three on the right are slit from strip. The curtain bracket part shown in the background can be produced by either of these methods.
For most narrow-width applications, slit strip can be the most economical selection. Slitting is done on efficient, precision slitting machines which can hold close-width tolerances and make multiple cuts in a coil.
However, when the part requirements demand deburred edges, a long continuous length without a weld, or a relatively small thickness-to-width ratio, flat wire may offer some advantages. These include longer continuous lengths; burr-free edges; or larger-sized packages of material.
The Basics of Rolling Flat Wire Strip
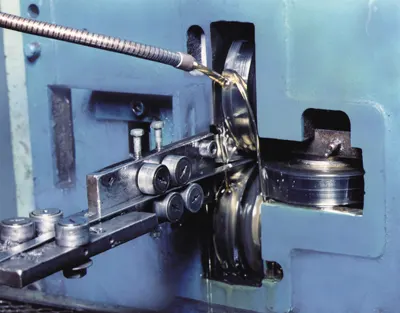
Flat wire is made by feeding rod of the appropriate diameter through a rolling mill, where it is flattened to the desired thickness. A set of opposing rolls in the other direction achieves the correct width and forms the edge, whether round square, or some special shape. Excellent control of width and edge condition are two of the advantages of producing narrow width strip in a wire mill.
The mill might be a multistand affair or, in the case of a turkshead mill, have all four rolls in a single bank of tooling. Some mills combine these two methods.
Flattened wire is just as easy to form or blank as strip of the same grade, but just like strip, there is a width-to-thickness ratio to consider. Most flat wire applications call for a material that is relatively thick compared to its width. Blanking is usually more difficult in flat wire than strip for that reason alone, but as you can see from the photograph at the beginning of the article, it is being done and with large blanks close to the edge.
Generally, fineblanking should be reserved for strip products.